Precast Equipment as Smart as it is Tough
Redi-Rock form and molds are expertly engineered and meticulously handcrafted to help you profitably produce the world’s leading precast modular block retaining wall system.
Forms
The Redi-Rock form is the core of your production and profit capabilities. Decades of continuous research and testing have resulted in a form optimized to produce better blocks with greater efficiency. Our northern Michigan-based team members handcraft the forms from the highest-quality steel, delivering you and your crew forms that meet your demands for long-term performance and durability. While 20+ years is a long time for a daily use form to remain operational, it’s worth noting that many original Redi-Rock forms – dating back to 2000 – remain in use still today.
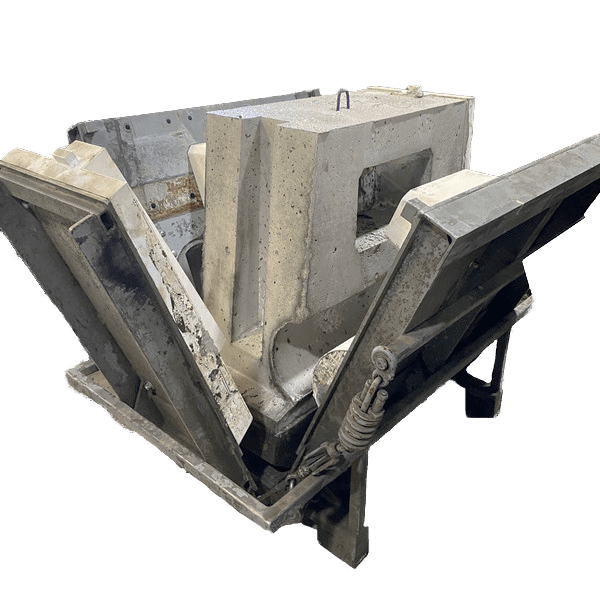
Retaining Form
The Retaining form produces blocks for constructing both gravity walls – the flagship solution of the Redi-Rock system – and mechanically stabilized earth (MSE) walls. These forms can host an optional insert, which casts a core slot into the block and produces a Positive Connection (PC) block. The core slot allows a strip of geogrid to wrap through the PC block during installation and then extend into the embankment, creating the reinforced zone for the MSE wall. PC blocks can also be used in gravity walls without the geogrid strips to create customized wall solutions tailored to specific site demands.
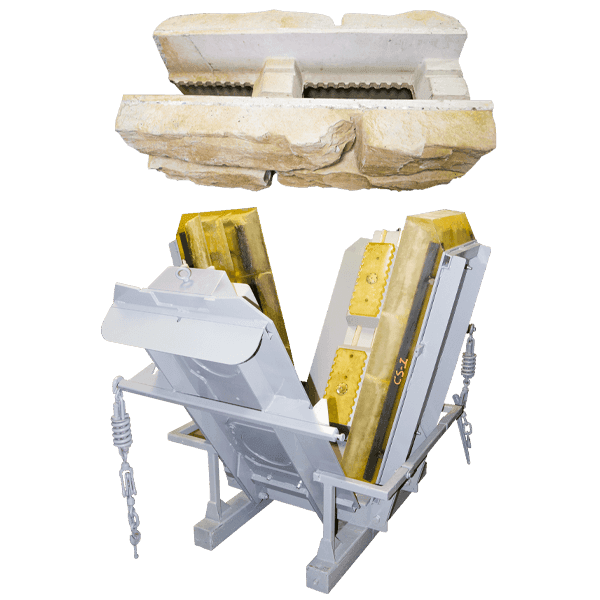
Freestanding Form
With the versatile Freestanding form, you’ll produce blocks featuring beautiful Redi-Rock textures on both sides. Freestanding blocks can be used for multiple applications, from constructing eye-catching above-grade walls for parking lots and trails to installing force-protection traffic barriers and stylish sign foundations. In addition to the standard solid block version, Freestanding blocks can also be produced in Hollow Core format and used to securely attach top-of-wall barriers like fencing.
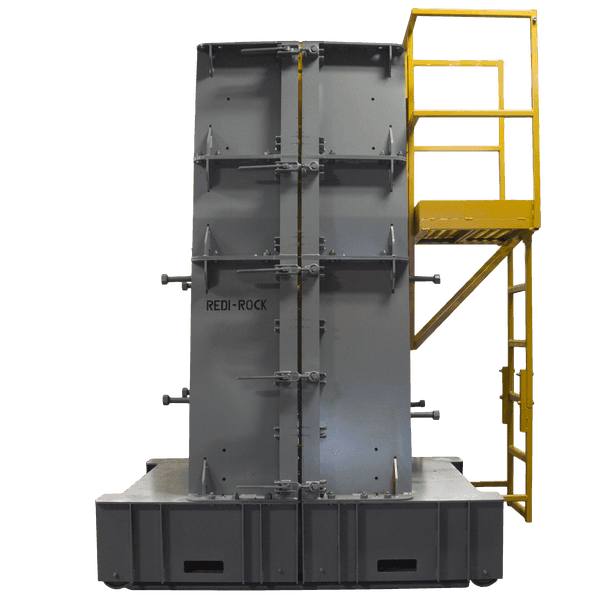
XL Hollow Core Form
With the XL Hollow Core block, you’ll reduce your material and transportation costs and maximize your customers’ installation efficiency. At 36 in (914 mm) tall and available in 52, 72, and 96 in (1320, 1830, and 2440 mm) widths, installers double their face coverage with each course. To ensure optimized wall designs, XL Hollow Core blocks are fully compatible with the remaining Redi-Rock product portfolio.
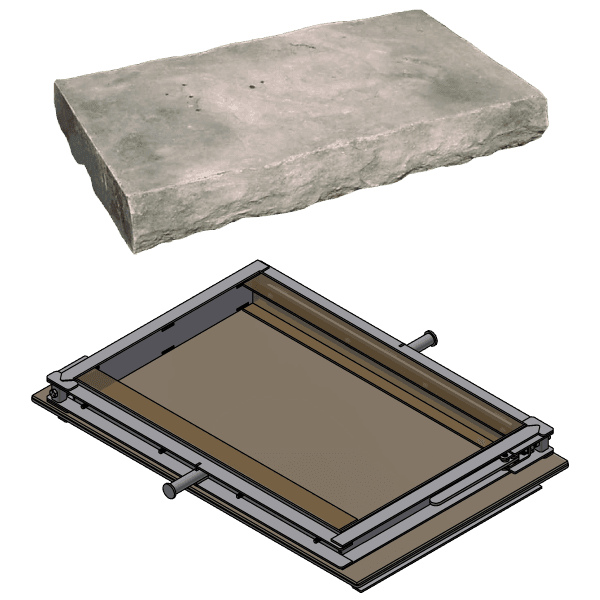
Step / Cap Form
The Step / Cap form produces the accessories that demonstrate the completeness of the Redi-Rock system. Steps and caps produced by this form coordinate beautifully with the Retaining and Freestanding Blocks to finish off projects and elevate them from functional to fascinating.
Molds
Redi-Rock molds deliver the finishing touches to projects that only natural stone can provide. Whether you’re supplying a detention pond for a new development, bridge abutments for a busy highway interchange, or a large retaining wall at a regional airport, you can be confident that your blocks will look just as good as they perform.

The Process
The textures you’ll produce look just like natural stone cut from the quarry. That’s because they’re modeled entirely after natural stone cut from the quarry. Rough edges, deep grooves, and irregular clefting are painstakingly reproduced to create the unique master mold used in the mold-making process.

The Materials
The polyurethane used to create Redi-Rock’s molds is a proprietary formula and the product of years of continual research and testing. These efforts have resulted in a polyurethane blend that effectively balances pliability, durability, and detail. With proper care and maintenance, you’ll produce great-looking Redi-Rock blocks for years to come.
Additional Equipment
To make certain you maximize your margins with efficient production practices and quality control measures, you’ll need some additional equipment.
6,000-lb (2722 kg) Forklift
You’ll employ your forklift to strip, transport, and stage your blocks. Keep in mind that the heaviest Redi-Rock block is 4,840 lbs (2190 kg).
Release Agent Sprayer
Your production team will spray the forms with release agent before each pour to ensure an easy release when curing is complete.
Form Vibrator
Precast concrete form vibrators evenly consolidate the mixture within the mold, promoting both the strength and aesthetic quality of the final product.
Flatbed Truck
You’re going to sell plenty of product and you’ll need a means with which to get it to the many project sites you’ll be supplying.
An Equipment Package Tailored to Your Market
Our team of experts will help you survey your preferred market to identify product demand, allowing you to build a production equipment package with confidence.
FAQ
What is the typical investment needed to begin producing Redi-Rock?
Multiple packages can be customized to address the needs of your market as you begin your Redi-Rock business. We’ve found most producers supply their markets over the short term with initial form and mold equipment investments of $90,000 - $100,000. Remember that additional equipment (pouring equipment, fork truck, etc.) is needed to produce. Contact us and we can provide more after learning a little bit about your plans.
How long do the rubber molds last?
The deep, natural texture of Redi-Rock blocks is created using a rubber mold that fits inside the steel form. Though it shouldn’t be expected, several initial Redi-Rock manufacturers still produce with the same rubber molds they purchased more than 20 years ago!
How long your molds last depends primarily on how you care for them. If you prioritize keeping the molds out of direct sunlight, storing the molds properly when not in use so they keep their shape, using the proper recommended release agent on the rubber, and cleaning them regularly, you’ll produce beautifully detailed Redi-Rock blocks well into the future.