Create Concrete Solutions
Manufacturing Redi-Rock retaining wall blocks is as simple as installing them. Learn about the production process of the world’s leading large block retaining wall solution.
The Production Process
Follow a Redi-Rock block’s production process from the cement drum to the inventory yard.
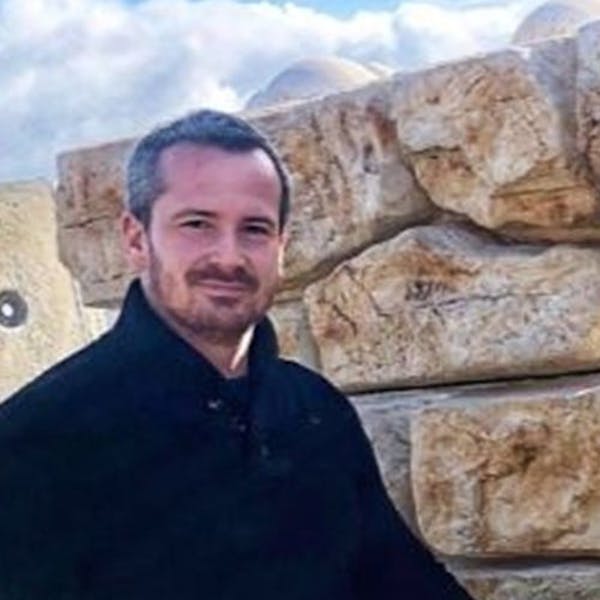
Almost every type of block can be produced with a single form style simply by adding inserts to customize the block type. To our company, this reflects Redi-Rock’s ongoing commitment to intelligent innovation and an efficient production process and adds tremendous value to our partnership.
Vincent Lachaux BBlox/Lachaux Betons (Saint-Pantaléon-de-Larche, France)
Precast Production Made Easy
Prepping the Form
Forms and molds are cleaned and any residue from previous pours is removed. A release agent is sprayed on the form’s inside surfaces to ensure blocks can be stripped easily once cured. The form is then closed and secured for pouring.
Inserting the Lifting Device
Lifting hooks are inserted in the concrete to aid in removing the cured block from the form and assist during project installation.
Pouring
The form is filled with wet cast concrete from a truck or hopper. Vibration is applied to the filled form to ensure proper material distribution and eliminate air bubbles. The top of the block is screeded to ensure a smooth surface.
Curing
Curing times vary based on the specific block produced, mix additives, ambient temperature, lifting device specifications, and other factors. Most producers double cast – or pour twice a day or more with a single form.
Stripping the Block
When curing is complete, the form doors are opened and the block is removed by an overhead crane or forklift, rotated, and placed on the production floor.
Transporting the Blocks
Blocks are moved to the inventory yard by forklift. This process is made easier and safer by Redi-Rock’s patented fork slots – grooves formed into the sides of each block. Multiple blocks can often be stacked to make this process more efficient.
Why Producing with Wet Cast Makes Sense
Redi-Rock is an intelligently engineered and simple-to-install earth retention solution. But its value isn’t limited to its smart features. Redi-Rock’s wet cast manufacturing process delivers production benefits dry cast simply can’t.
Wet Cast is Less Expensive to Produce
The equipment necessary to produce wet cast products is much more scalable than dry cast systems. Wet cast does, however, require extended time for curing, giving dry cast a slight edge in pace of production.
Wet Cast is Easier to Customize
Wet cast’s consistency allows for the production-stage inclusion of customizations that engineers demand for important jobs. Dry cast’s high-compression production process doesn’t permit the same level of product customization.
Wet Cast Production Demands Less Space
Dry cast concrete can’t be poured from a truck making an on-site batch plant a necessity. Wet cast is much more flexible in its mixing and conveyance, allowing it to be prepared offsite and delivered to production.
Planning Your Production Facility
With more than 130 producers and nearly 170 manufacturing locations worldwide, we’ve consulted on and observed countless manufacturing facility configurations. The sample production floor diagram highlights one option for possible equipment placement. You’ll also have access to extensive support resources developed to help you select an equipment layout and production process tailored to your specific space and goals.
See How Redi-Rock Can Work for You
Redi-Rock isn’t a one-size-fits-all product or process. It’s successful because it’s adaptable and scalable. Can we customize a Redi-Rock production scenario just for you?
FAQ
How is Redi-Rock produced?
Redi-Rock production is straightforward, just like your customers will find its installation process.
- Prep the forms with release agent and color (if desired)
- Pour the forms with concrete and vibrate
- Let the product cure
- Strip the blocks from the forms
- Transport the blocks to inventory with a forktruck
- Clean the forms and repeat
And just like installation, the production of Redi-Rock only requires a small crew.
How much space do I need to produce Redi-Rock?
The answer to this question depends on your desired product mix, the number of forms you’re working with, and the automation level of your production process. To give you a rough idea, we can share a production floor measuring 35 ft x 45 ft (10.7 m x 13.7 m) can generally accommodate a standard mix of eight retaining block forms, two freestanding block forms, and one step/cap form.
We’re always excited to discuss production scenarios with you. Contact us and we’ll follow up with you promptly.