Production Process: Grow Your Business One Block at a Time
With the Redi-Rock forming system, you'll be the one-stop shop in your markets for engineers that need retaining wall solutions. You can provide an array of products to build tall gravity walls, even taller reinforced walls and enough accessories like steps, caps, and columns to finish off every project with style. See how easy it is to diversify your product mix and grow your business one block at a time.
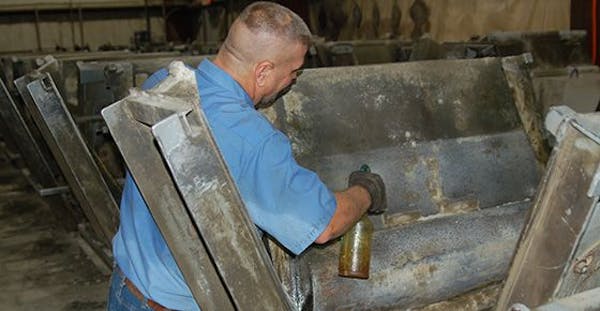
1. Prep the Form
Preparing the forms for production is a very important step. Items that need to be addressed include:
- Cleaning the forms to ensure there is no residual concrete that could prevent the forms from closing properly
- Spraying recommended release agent to ensure that the blocks can be easily removed from the forms
- Applying shake-on color hardeners if blocks are being colored
- Closing the forms and ensuring that they are properly secured
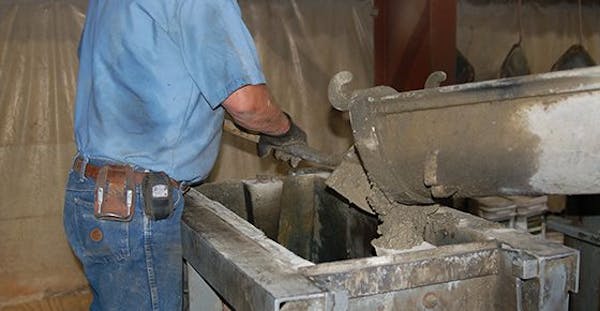
2. Pour the Block
A crew can pour wet-cast concrete into a Redi-Rock form using several methods, including from a cement truck or a hopper from a mixer.
If a shake-on color hardener is used, it's important to protect the color by using a shovel to disperse the concrete as it's poured into the form.
Vibration is then required for concrete distribution. If Self-Consolidating Concrete (SCC) is used, this step is omitted.
The last step in pouring a Redi-Rock block is screeding the top of the block to ensure a smooth surface and cleaning the concrete off of the rest of the form.
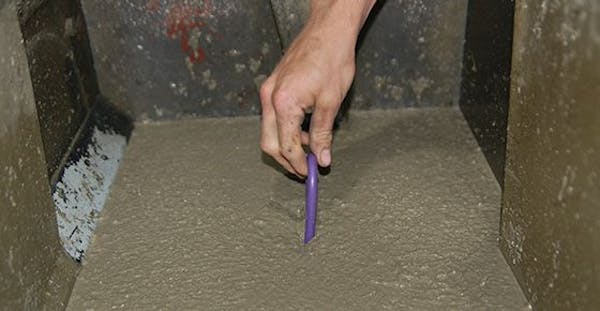
3. Insert the Lifting Device
Inserting a lifting device before the concrete cures is very important, as this is how the block is removed from the form after it has cured. These lifting hooks are often used in the installation phase of a project as well. Most Redi-Rock products use one lifting device in the back of the block; however, the Positive Connection System uses two lifting devices.
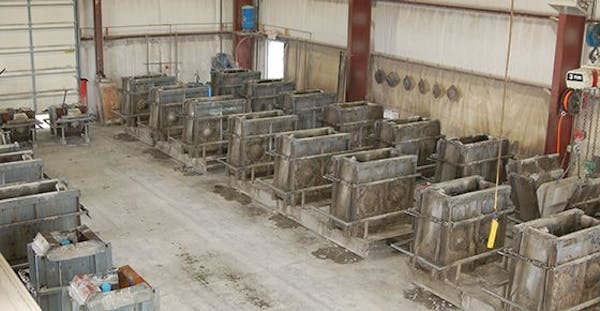
4. Let the Block Cure
After the block is poured, the product must cure enough to maintain the integrity of the block from damage and cracking if pulled too green. The time is dependent on any additives used in the mix design to accelerate the curing process, ambient temperature, lifting device specifications, and several other factors. It also depends on any project-level specifications that require certain hours in the form before they are pulled. SCC is used by several existing Redi-Rock manufacturers as well.
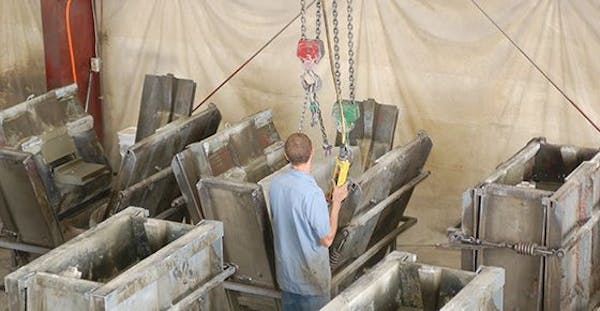
5. Strip the Block
After the block is properly cured, open the form doors and remove the block from the forms by placing a chain into the lifting device in the back of the block. Removal can be accomplished by a 6000# forklift and an approved chain or by an optional overhead crane with coffing hoist to rotate the block in the air and place it properly on the ground.
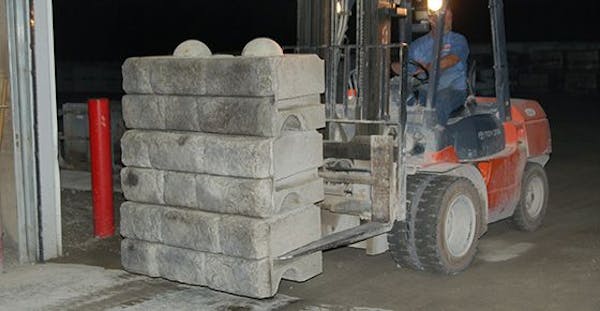
6. Transport Blocks to Inventory
Blocks are then transported to inventory or the staging area. This is most commonly done using the patented fork slot on each block and a fork lift. Multiple blocks can be stacked on top of each other to maximize efficiency.
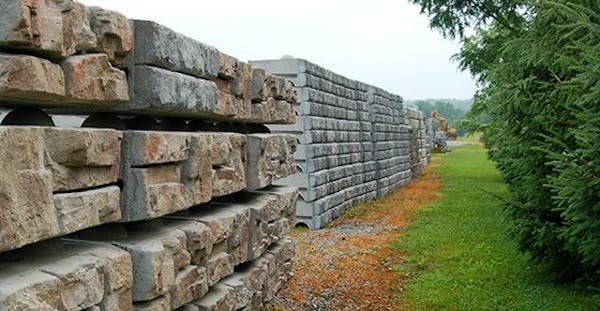
7. Inventory the Blocks
Maintaining adequate inventory is very important to the Redi-Rock business. It is recommended that a minimum of 3 month’s supply be kept in inventory to ensure you can meet the demand for emergency projects.